Thermal processing in a retort is a complex world. Its correct approach leads to success in extending the shelf life of canned foods and their preservation and avoids headaches when the product is already in the consumer chain. It also allows increasing the useful capacity of the retorts when it is correctly designed and specified.
To answer the most typical questions that we receive from our clients regarding thermal processes, we have addressed them to one of the most important references in the world of sterilization, the Thermal Process Specialist, Clara Rovedo, from the Klaratech company, located in the heart of Europe.
Clara, based on your experience, what are the most frequent concerns of your customers regarding thermal processes?
Most customers know their processes pretty well and turn to a Process Authority when they face process deviations in their retorts that they do not know how to manage or identify. The most frequent concerns have to do with changes in the facilities that affect the process variables, not knowing where the sterilization recipes come from, or not having process letters or thermal distribution studies.
New customers are concerned about how to ensure that they have achieved commercial sterility in their product, that they have reached the target Fo and that they will not have public health problems.
Another big concern is how to deal with the USFDA, but I'll answer that in the next few questions.
I never did a thermal validation of my retorts process. What is the worst that can happen to me? How do I take my first steps?
Sterilization in a retort is the most critical process on the production line. The customer should thoroughly understand that a contaminated product can put people's health at risk, even to the point of causing death. Thermal processes may have always deviations, no matter how thoroughly they are known or if they have been done in the same way over the years. The client must know how to understand where these deviations come from and how to manage them. Therefore, they must know their processes, thermally speaking.
The first step is always to question yourself. Where did we get the sterilization recipe from? Why is it like this and not that other way? Have we changed the variables or the installation over time? Then the next step is to do thermal distribution and heat penetration studies and repeat them with a certain periodicity.
In your opinion, when is the intervention of a Process Authority strictly necessary?
Generally, the one who takes care of thermal processes in the industry is the Quality Department, or even the figure of the Thermal Process Technologist. That is excellent and it should be that way, although if the involved persons do not have enough know-how or come from other areas or other types of industries, it is advisable to turn to a Process Authority to provide the appropriate advice, so that they can continue the steps by themselves afterwards.
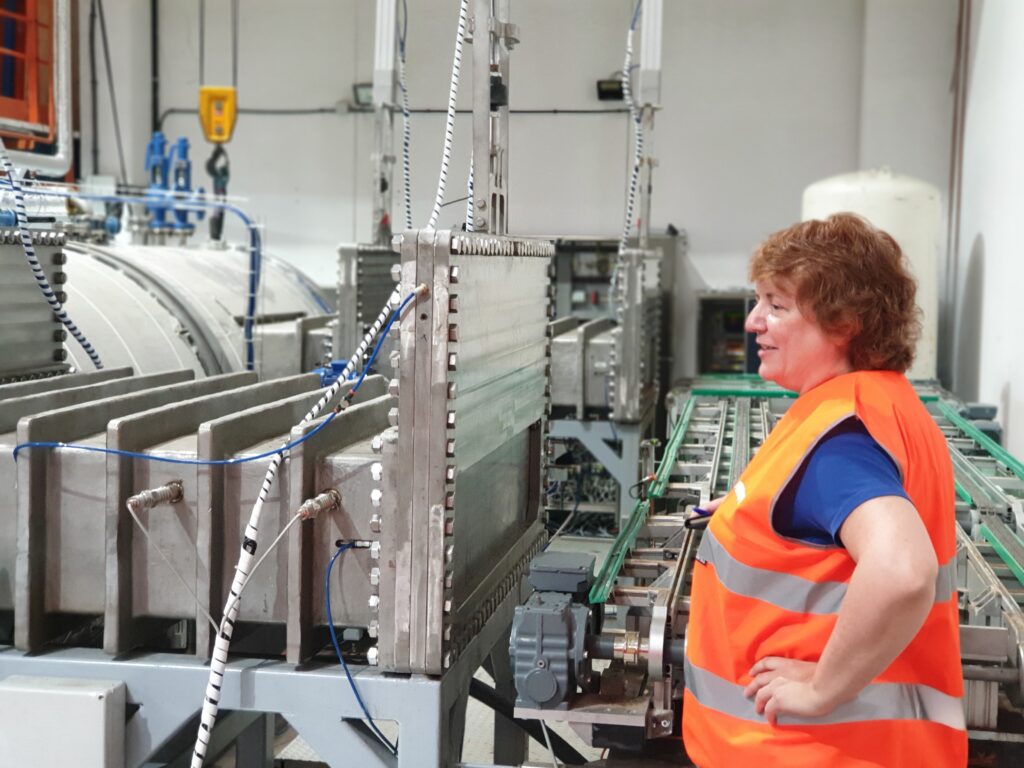
<<The Process Authority is a figure that accompanies the client in terms of thermal processes, advising and supporting them on how to take steps the most safely and efficiently way possible. It should never be viewed as an authority figure or statutory audit, but rather as a source of expertise and consultation.>>
Another opportunity to turn to a Process Authority is when you are going to produce or export to a market that has certain requirements of its Food Administration, for example, the FDA in the USA. This agency requires the intervention of a Process Authority to approve the products. Process Authorities do not have a title as such, but agencies like the FDA require that we be recognized by our peers. Therefore, it is healthy to consult with a couple of sources, the reliability of who calls himself Process Authority.
Do you think there are preconceptions in the industry when it comes to call a Process Authority? Which ones?
Yes, I think that the name "Process Authority" is not very favorable, since clients think that we are a kind of Auditors who are going to remark the deficiencies of their process and highlight things that are being done wrongly. And it is not like that. The Process Authority is a figure that accompanies the client in terms of thermal processes, advising and supporting them on how to take steps the most safely and efficiently way possible. It should never be viewed as an authority figure or statutory audit, but rather as a source of expertise and consultation.
<<[...] it is healthy to consult with a couple of sources, the reliability of who calls himself Process Authority.>>
Could the useful capacity of the retort be optimized through a comprehensive thermal study?
Yes, of course. If retorts represent a bottleneck, there are always possibilities to optimize the cycles in terms of sterilization, as long as we refer to the coldest point inside the vessel. We must know well the Fo target, where we must reach it and go for it at that point. The process will already be safe if these conditions are met, it is not necessary to over-sterilize 'just in case'.
It is important to note that many times the retort control is the one that lowers the quality of the process. Ideally, the controls should be developed by the retort manufacturer, as he knows the equipment better than anyone. If the controls are developed by another company, that company should be familiar with how the retort works to prevent the process from being inefficient.
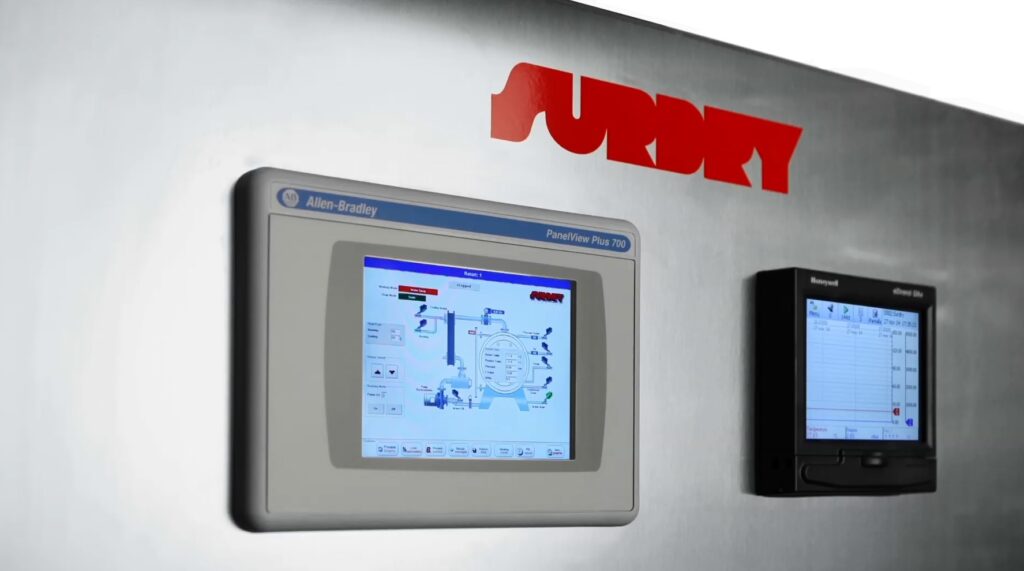
Could a thermal process advice determine that the retort is being used incorrectly?
Yeah sure. In my career I have come across many cases in which certain sterilization recipes seem to be inscribed on stone and to be sacred, being passed down over the years, even between companies. This is a total risk. It should always be clear that each retort, each product and each installation are unique and unrepeatable. What works well in another company or in a copacker will not necessarily be the right thing in my process.
Is there a sterilization method that is safer than another?
Today most of the retorts on the market fulfill their mission, to a greater or lesser extent. It is true that of all the existing processes, I feel more comfortable with the Steam & Water Spray because I know that it will work correctly for sure and have a magnificent thermal transfer. This is probably why it is a very popular process in the USA, for example. Either way, all technologies have their pros and cons.
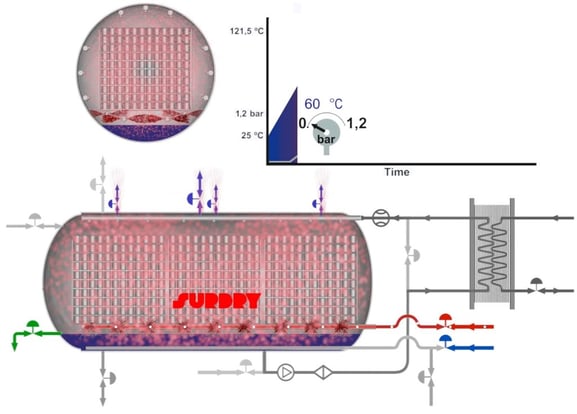
I have to recall my products because there have been food safety issues in the market. How do I know if it may be related to my retort process? Where do I begin?
When there is a recall of my products, the first thing I should analyze is the process reports from the retort. I should know what happened to that batch that day, and if there were any deviations. If we do not see anything strange in the process, there may have been problems with the ingredients or the filling, upstream of the retort. Post-process contamination issues should be also considered.
If you had to talk about an experience in your career that has forever marked the way a client of yours works, what would it be?
I remember I received a call from a customer in Brazil that produces dairy products in cans. They were desperate to solve a product contamination problem. They thought it was attributed to improper sterilization and that is why they called me. I traveled, we did all the pertinent measurements and studies, and the retorts were working perfectly. We took a tour within the factory and they told me that they made their own cans. Out of curiosity, I started to ask them if they had made any changes to the can manufacturing and they told me that, for some time now, they were gradually reducing the thickness of the metal to save costs. I asked them to make thicker cans and see the results. The problem disappeared! What it was happening is that they had changed the resistance of the container but the retort had never been aware of this change and the overpressure was not enough. The cans would swell and then when cooled they probably returned to their original shape. However, they had post-process contamination problems because the cans and seals were not sufficiently resistant to the thermal process.
<<It should always be clear that each retort, each product, and each installation are unique and unrepeatable. What works well in another company or in a copacker will not necessarily be the right thing in my process.>>
I produce in the USA or I want to export my products there and I will need to register them with the USFDA, how do I get started?
It is in this process that the Process Authorities become essential. Not just for advice but because the FDA needs to see strong data and support from a recognized authority. Therefore, my first recommendation is to turn to a Process Authority. As I mentioned earlier, you should be careful with the source. There are many companies or organizations that call themselves Process Authorities but they are not really prepared for this challenge. The FDA requires that we be recognized by our peers, so if clients want to save themselves from paying twice for advice, it is healthy to consult different sources about the recognition that that Authority has.
In general, the steps to follow are:
- Register the company with the FDA
- Carry out the temperature distribution and heat penetration studies for each retort and each product (note: a product as such is the combination of the container plus its content).
- Register the products to be produced/exported, attaching the process letters, temperature distribution and heat penetration studies, along with all the relevant documents in each case.
The goal is to submit each case correctly and clearly, in order to minimize or avoid further inquiries by the FDA.
Finally, if you had to give your best advice to customers who are reading this, what would it be?
My best advice would be not to assume that you know everything about the thermal process of each product. The healthiest thing is to question everything. What is the origin of my sterilization recipe? Is it the correct recipe? Why the thermal steps are these and not others? Is the Fo reached the right one for my product? Can I improve it and make it more efficient? If the answers to those questions are not clear or forceful, then you should take action.
<<The healthiest thing is to question everything.>>
Ask for an assessment with your Process Authority or contact us for support!
If you have any questions you may address them directly to Clara Rovedo at:
+32 495 12 49 95 crovedo@klaratech.com Klaratech BVBA 9140 Temse, Belgium |